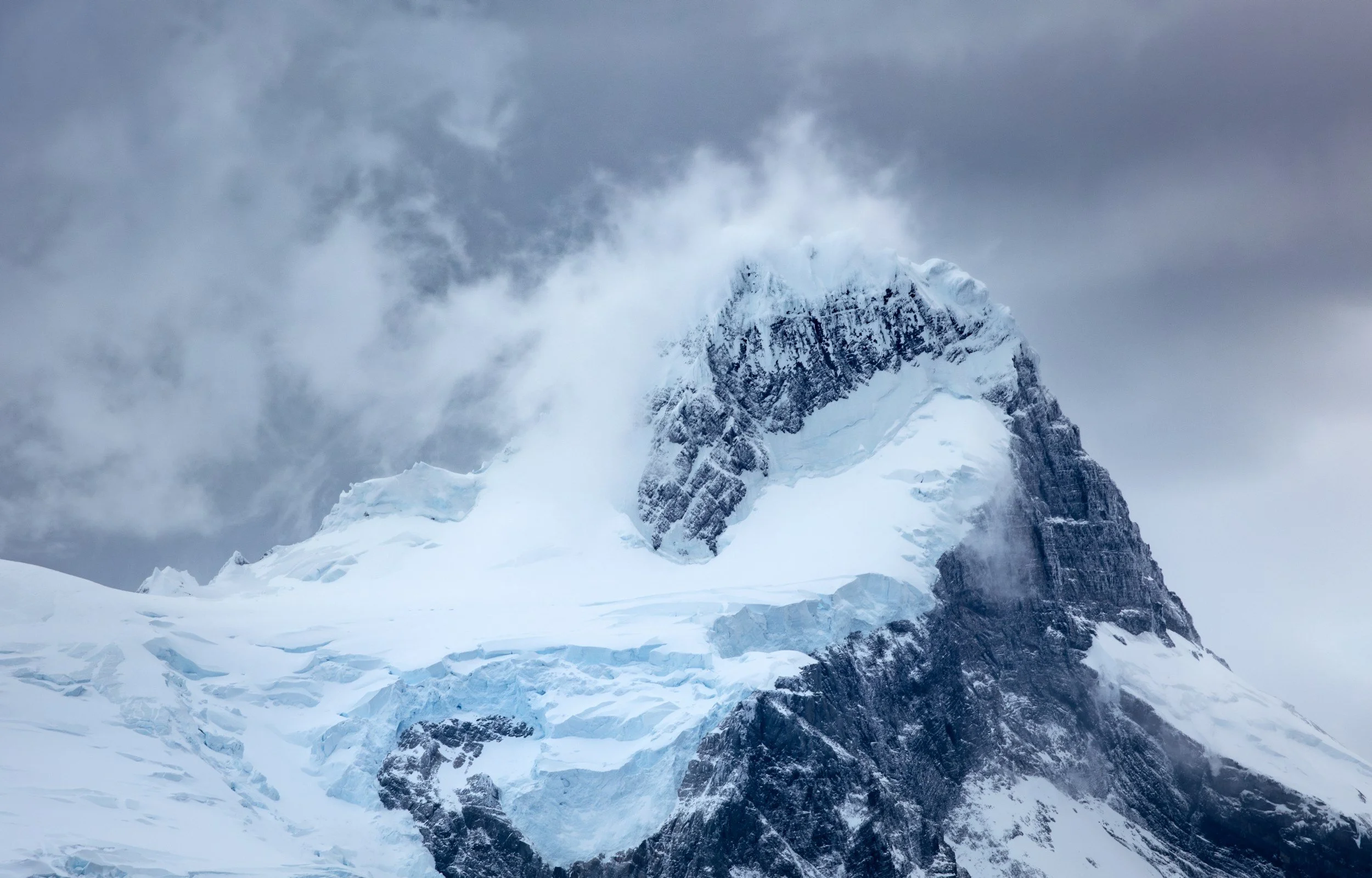
“The best way to predict the future is to create it.”

NASA
Research, Innovation and Design
"Imagine a spacecraft millions of miles from Earth, its critical electronics on the verge of overheating—a single failure could doom the mission. That’s the problem I set out to solve as the leader of Team’s Self-Healing Thermal Management System. Frustrated by the limitations of traditional cooling methods, I pioneered a breakthrough solution: microfluidic channels infused with graphene nanofluids and self-healing polymers, enabling autonomous repair of thermal damage while dissipating heat 50% more efficiently. From conceptualizing the serpentine channel design to leading a cross-functional team in prototyping and testing, I bridged materials science, fluid dynamics, and embedded systems to create a lightweight, NASA-aligned technology that extends mission lifespans and slashes costs. This project wasn’t just about engineering—it was about redefining resilience in extreme environments. Now, I’m driven to bring the same relentless innovation to product design challenges in the corporate world, where user needs and cutting-edge technology collide. Let’s build the future, one thermal hotspot—or one brilliant product—at a time."
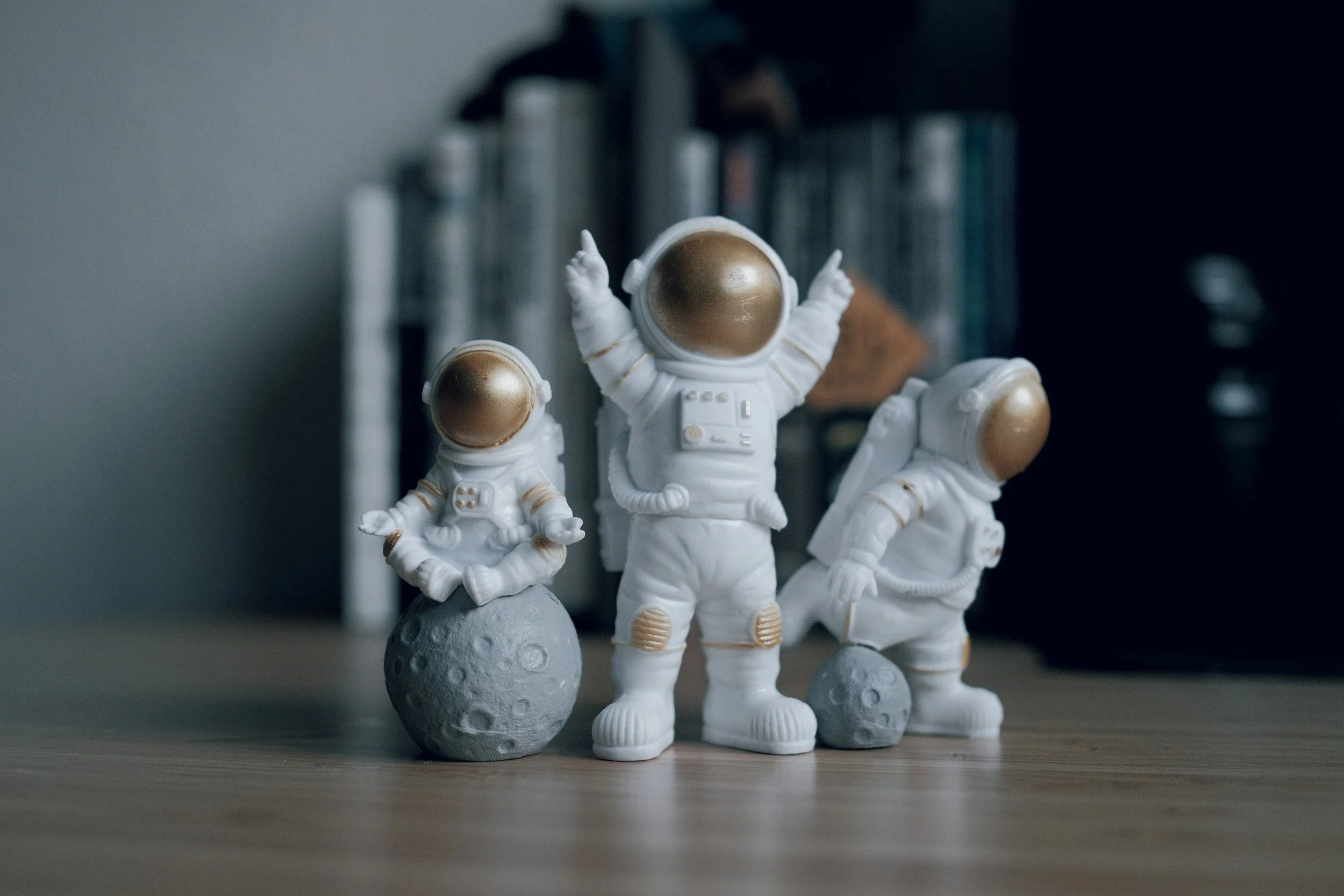
Project Title: Self-Healing Thermal Management System Using Nanomaterial-Infused Microfluidics
Role: Principal Investigator & Project Lead
Overview
Spearheaded an innovative thermal management solution designed to address critical overheating challenges in spacecraft electronics. This groundbreaking system integrates graphene-infused nanofluids with self-healing polymers within a microfluidic network, enabling autonomous repair of thermal damage while enhancing heat dissipation in extreme space environments. The project aligns with NASA’s mission to improve reliability, longevity, and cost-efficiency for long-duration space exploration.
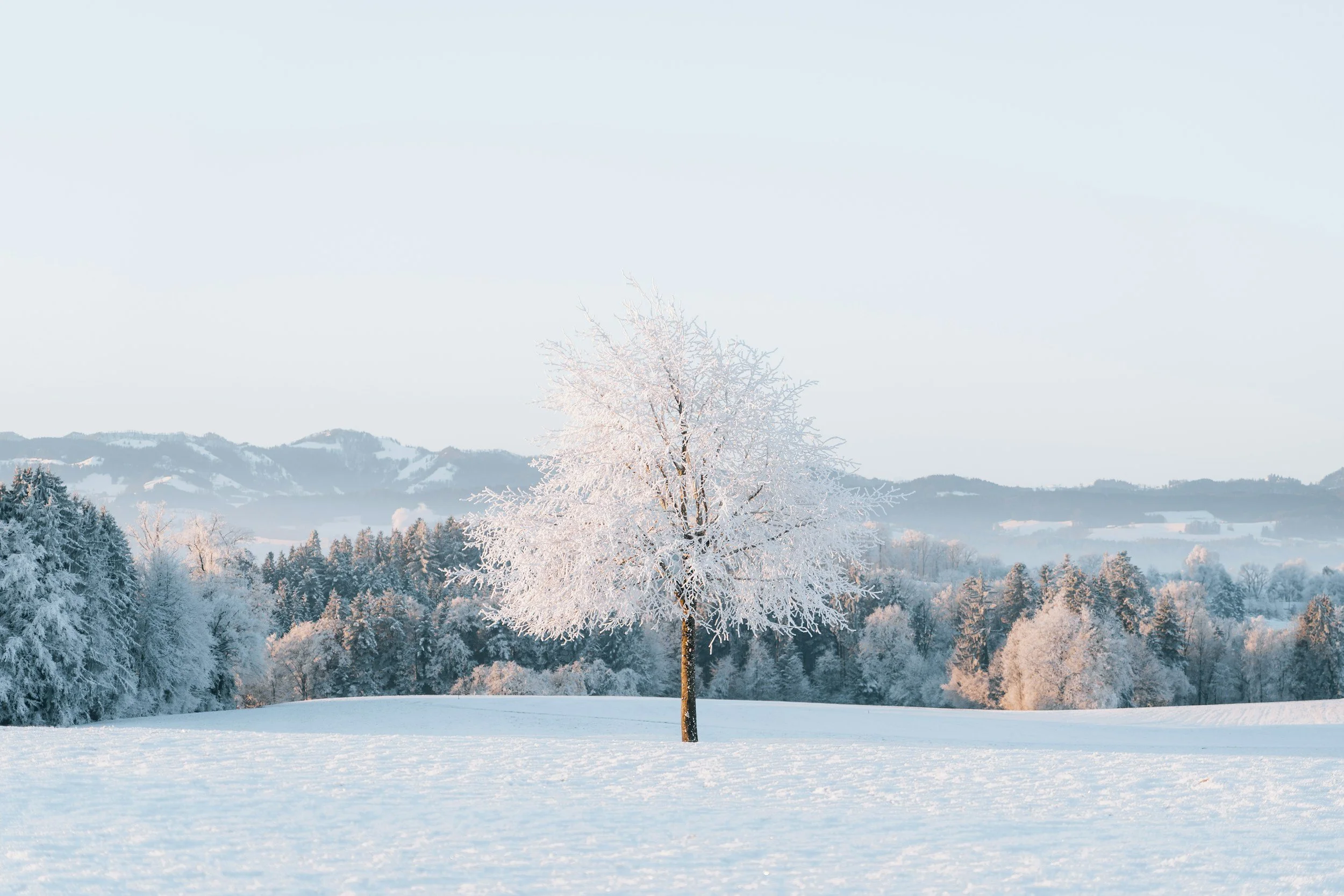
Make it stand out.
Key Innovations:
Self-Healing Capability: Utilized polyurethane-based polymers to autonomously repair microcracks and thermal deformations, significantly reducing maintenance needs and extending system lifespan.
Nanomaterial-Enhanced Cooling: Incorporated graphene-coated microfluidic channels to maximize thermal conductivity and heat transfer efficiency, outperforming traditional passive systems.
Lightweight & Scalable Design: Engineered with 6061-T6 aluminum alloy for optimal thermal performance and weight savings, ensuring compatibility with spacecraft constraints.
Adaptive Thermal Management: Implemented electroosmotic pumps and serpentine microfluidic patterns to dynamically regulate heat distribution, addressing localized hotspots in real time.
Achievements & Impact:
50% Longer Electronics Lifespan: Demonstrated potential to extend operational longevity of onboard systems through superior heat dissipation and damage mitigation.
30% Cost Reduction: Projected significant savings over conventional thermal systems by minimizing failures and manual interventions.
NASA Roadmap Alignment: Directly addressed taxonomies TX12.3.4 (Reliability), TX12.2.1 (Lightweight Concepts), and TX13.1.7 (Radiation Resistance), positioning the technology as a transformative solution for future missions.
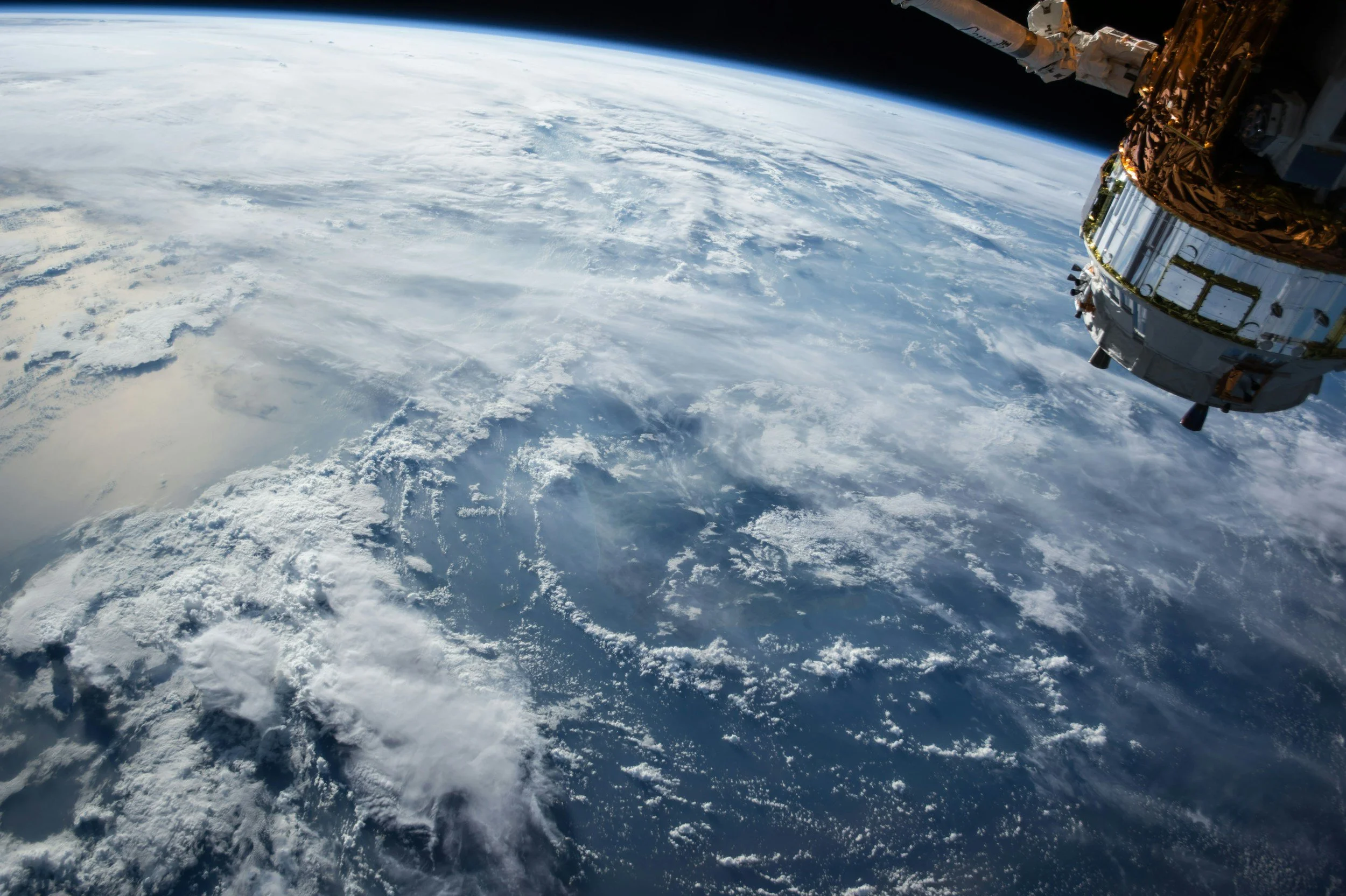
WHY IT STANDS OUT
This project merges cutting-edge nanomaterials, autonomous repair mechanisms, and scalable microfluidics to solve a high-stakes challenge in aerospace engineering. Its creativity lies in the synergistic combination of emerging technologies, while its practicality is proven through rigorous simulation and prototyping. The system’s potential extends beyond NASA to high-performance electronics, defense, and automotive sectors, showcasing versatility and market viability.
Collaboration & Leadership:
Led a multidisciplinary team of 10 researchers across 6 institutions, coordinating roles in engineering, materials science, and business analysis.
Partnered with Dr. Sunand Santhanagopalan (UT Arlington) to refine nanomaterial integration and microfluidics performance.
Secured $3,500 in budgeted resources, leveraging university facilities for cost-effective prototyping.
Deliverables:
Functional prototype of a lightweight, self-healing microfluidic cooling system.
Computational models and test data validating performance in extreme conditions.
Cost-benefit analysis demonstrating long-term mission savings and reliability gains.