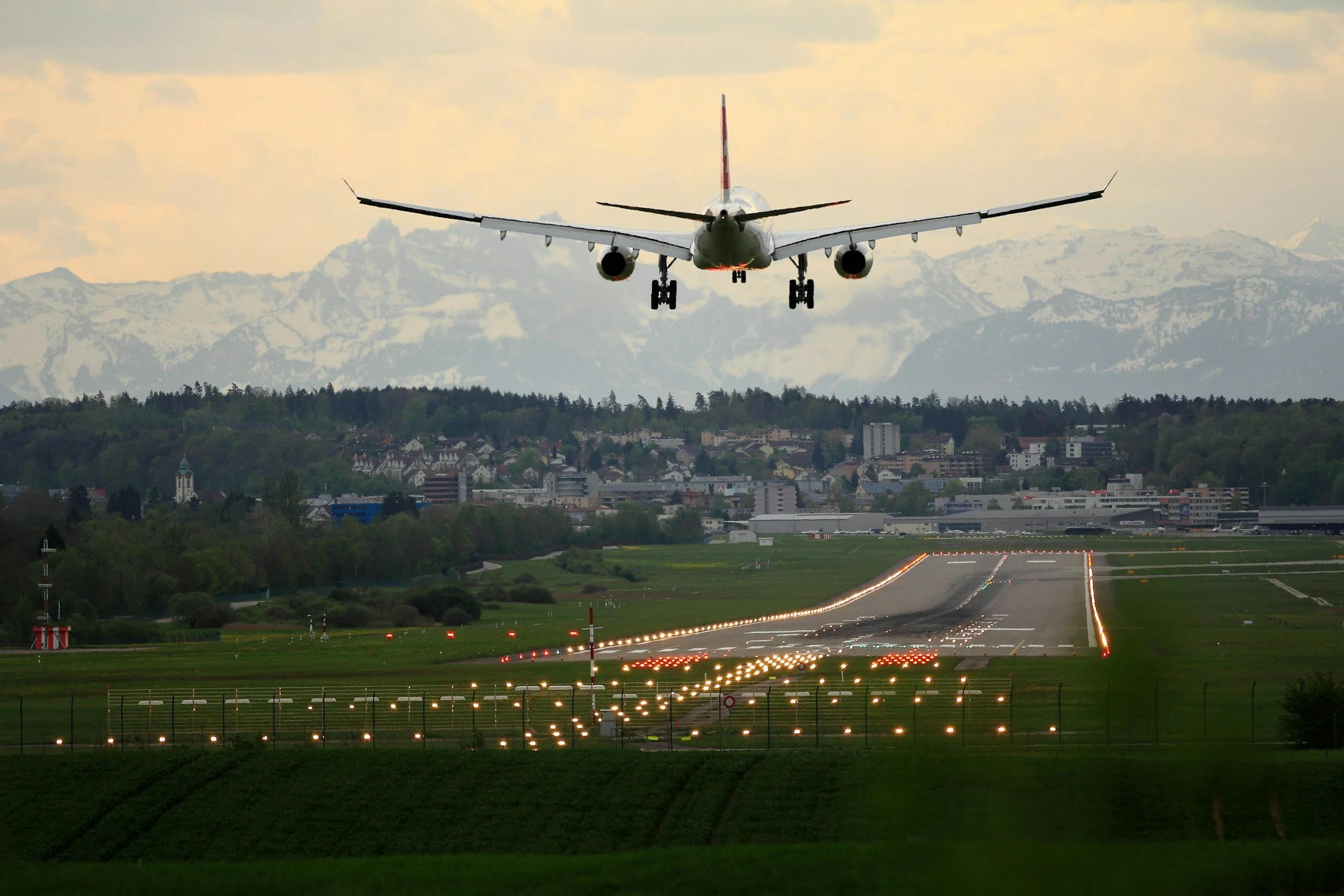
Aeroelasticity and Deformation Analysis of a Convergent-Divergent Nozzle Using ANSYS Workbench
This research investigates the aeroelastic behavior and structural deformation of a De-Laval convergent-divergent (C-D) nozzle, a critical component in aerospace propulsion systems. The study focuses on fluid-structure interactions, flutter effects, and structural integrity under extreme aerodynamic and thermal loads.
Industry Relevance
C-D nozzles are integral to rocket propulsion and supersonic aircraft, where maintaining structural stability and efficiency is crucial for mission success. The research addresses industry challenges such as flutter-induced vibrations, pressure-induced deformation, and material optimization to enhance nozzle durability and performance.
Methodology
Computational Fluid Dynamics (CFD) Simulations: Conducted using ANSYS Fluent to analyze supersonic flow behavior, pressure variations, and Mach number effects.
Finite Element Analysis (FEA): Performed in ANSYS Static Structural to evaluate deformation, equivalent stress, and structural responses.
Fluid-Structure Interaction (FSI) & System Coupling: Integrated analysis of fluid dynamics and structural mechanics to simulate real-world operational conditions.
Material Selection & Optimization: Evaluated titanium alloys and superalloys for lightweight, high-temperature resistance, and mechanical robustness.